Engineering & Simulations
We offer support in construction or we will take your project into our own hands. If you need a single-purpose device, we are here for you. We will design a device according to your ideas and requirements
Design
After a closer acquaintance with your requirements, we will design the equipment and give you a non-binding quotation.
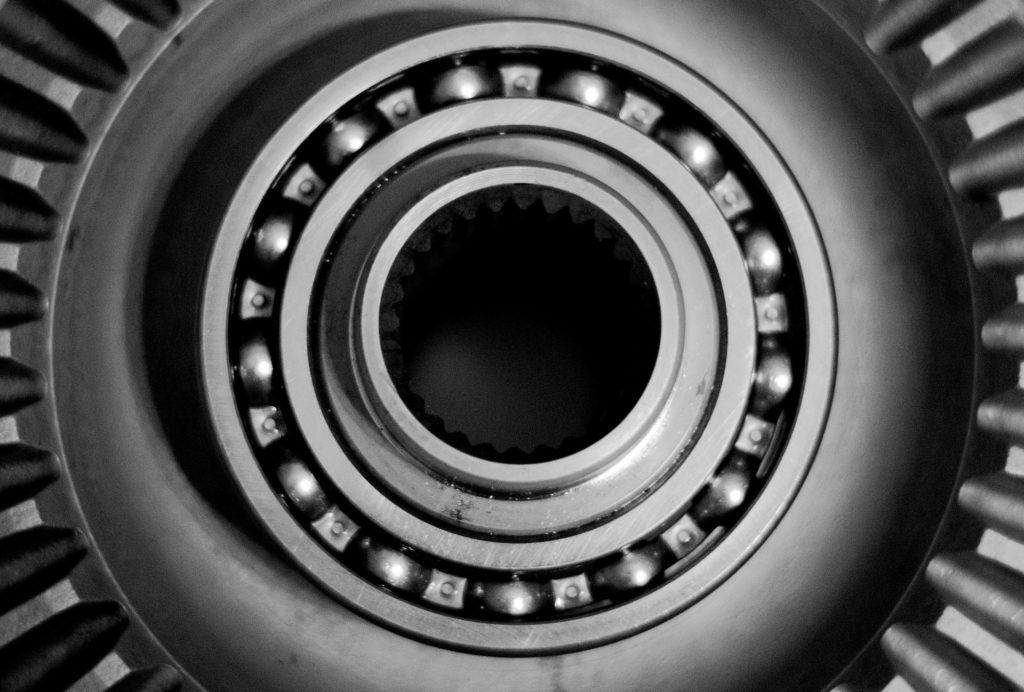
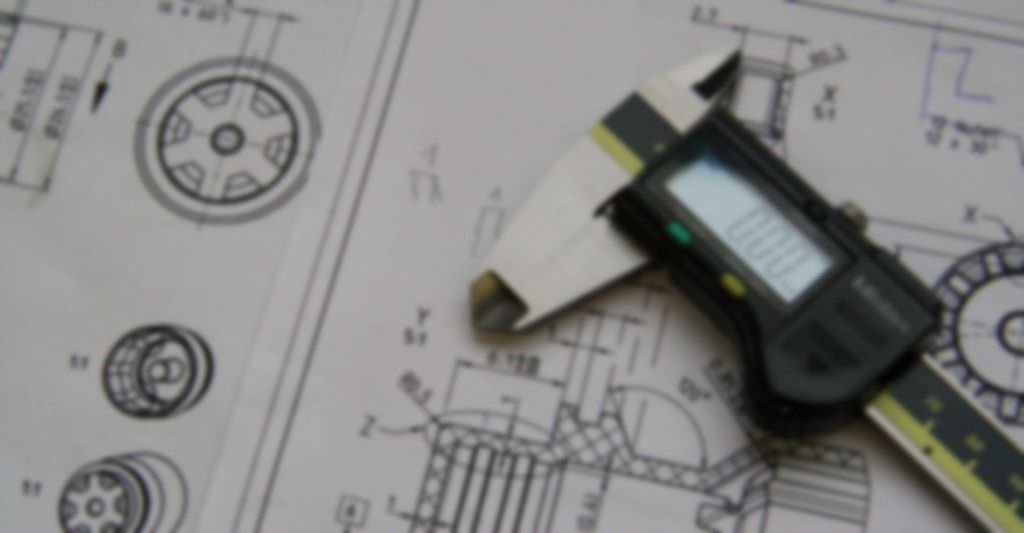
Delivery
We will provide you with drawings in the form of digital data and also drawings in paper form
Simulations
The simulation itself takes into account the loads acting on the product. Using finite element modelling (FEM), your 3D model is divided into small elements, which then form the finite-element model. Forces and loads are applied to this model and the result is the stress distribution in the case of strength analysis. If we are talking about dynamic analysis, first the natural frequencies of the model are calculated and then the response of the product to the different frequencies. The thermal analysis is used to verify the functionality when exposed to thermal radiation and or when conducting heat through the product.
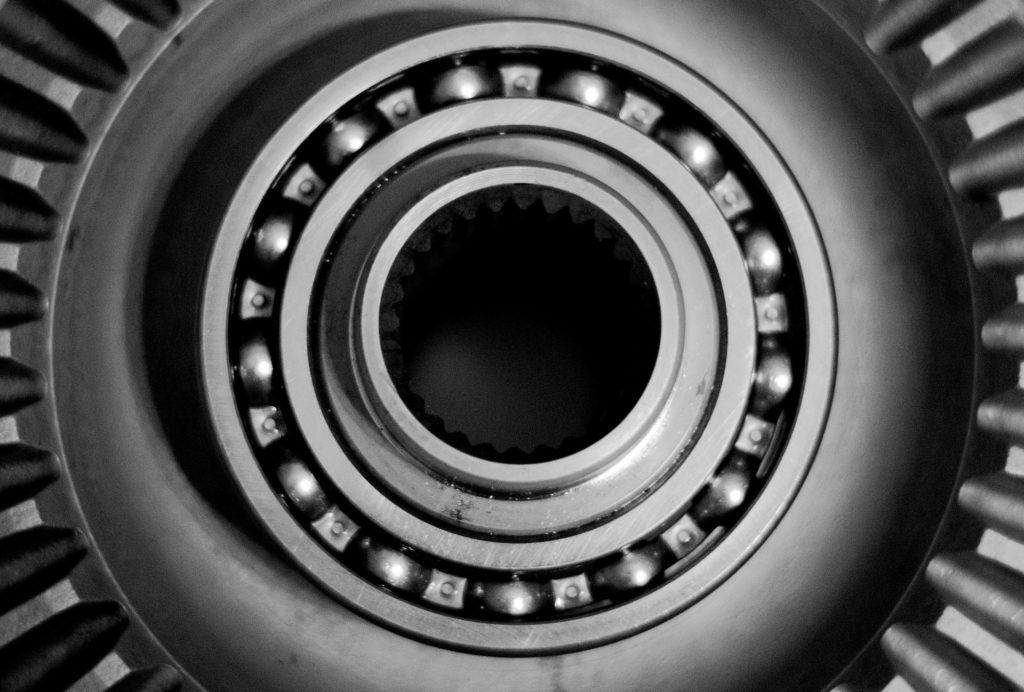
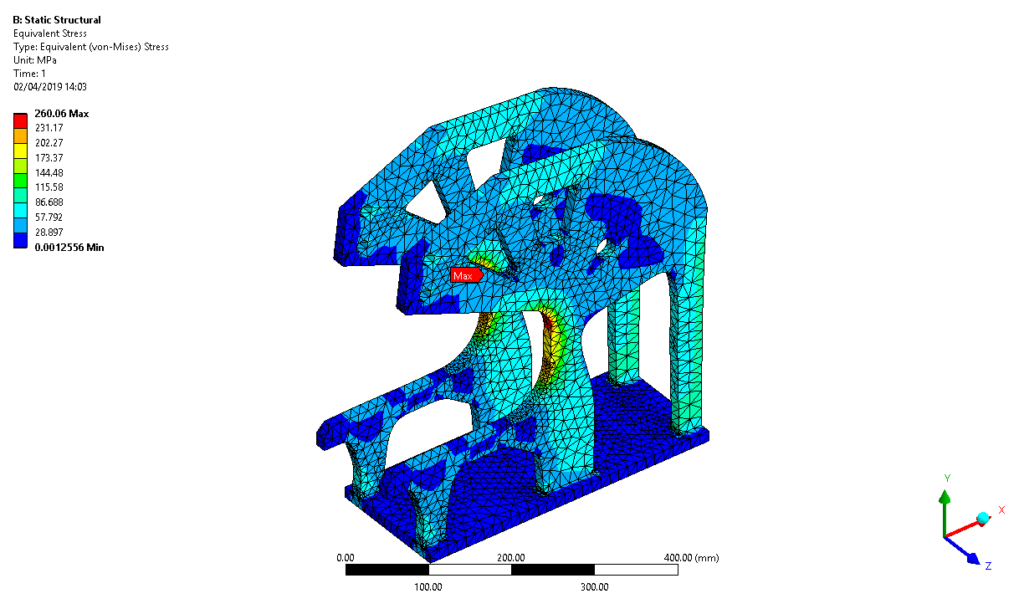